1. INTRODUCTION
1.1. One of the most important quality management legs is the implementation and the aim to establish, maintain, and increase customer satisfaction as well as meet international standards and OEM requirements.
1.2. This manual aims to complete the Loran Aerospace Terms and Conditions of Purchase and Supplier Charter, and the manual has been implemented to establish the control of suppliers' processes and products, which have a potential impact on the conformity of products supplied by Loran Aerospace (LORAN).
1.3. The suppliers of LORAN are responsible for their performance in terms of Quality, Cost, Delivery and commit to:
1.3.1. implement the organization and the necessary means,
1.3.2. guarantee the quality of their products and delivery times,
1.3.3. measure and optimize their quality and logistics performance, both internally and externally,
1.3.4. contribute to joint quality and logistics actions with LORAN.
This supplier involvement is reflected in the application of this manual and its updates.
2. PURPOSE
2.1. The purpose of this manual is to:
2.1.1. define Loran requirements, complementary to international standards and applicable regulations,
2.1.2. flow down the requirements of Loran’s customers,
2.1.3. introduce the process of supplier approval and product/process qualification,
2.1.4. describe methods for monitoring performance throughout the product's life cycle (development and serial).
3. DEFINITIONS AND ACRONYMS
3.1. LORAN: Loran Aerospace Incorporated
3.2. Supplier (Seller or Vendor or Sub-Contractor): business organizations that can provide products or services for LORAN.
3.3. Product: The service or equipment considered or ordered to be purchased by LORAN.
3.4. PO: Purchase Order
3.5. Supplier Code of Conduct (SCC): expresses Loran Aerospace's expectations for our suppliers and mirrors our Quality Management System requirements standards.
3.6. FOD: Foreign Object Damage or Foreign Object Debris
3.7. CofC: Certificate of Conformance
3.8. Mandatory: Minimum requirements for qualification
3.9. Primary Preference: Reason for choosing the supplier as a priority
3.10. Project Management Possession Documents: All types of documents, including traceability, quality control, financial, and CofC, obtained by the supplier while processing a project for LORAN.
3.11. On-Site Acceptance: The product acceptance process is performed at the supplier's place before dispatching.
3.12. QC: Quality Control
3.13. The National Institute of Standards and Technology (NIST): is an agency of the United States Department of Commerce whose mission is to promote American innovation and industrial competitiveness.
3.14. Traceability: The term is a capability to track and document the history, location, and (if exist) usage of the product or the materials from the manufacturing stage to (if exist) the distributors/suppliers and to the current end-user.
3.15. Certificate of Origin (CofO): It is an origin country declaration for the supplied product.
3.16. Certificate of Conformity (CoC/CofC): It is also known as a Certificate of Compliance or Certificate of Conformance and is a document that verifies that a product or service meets required standards or specifications. Loran carries out its policy covering the preparation, preservation, and transmission of CoC documents to the customer in accordance with the AS9163 2022-12 Standard.
3.17. Purchasing Exception: If the product is not available from another company in the market, or the product is "hard to find", or the customer has a special supplier request for the product, Loran carries out the product order subject to the approval of the top management, except for the supplier being an "approved" supplier. These suppliers are classified as "Conditionally Approved" suppliers for Loran. If traceability is unavailable or the documentation is suspected of being falsified, Loran discontinues efforts to procure the part.
3.18. NDT: Nondestructive Test
3.19. DT: Destructive Test
3.20. Configuration is a documented information that covers the technical and physical specifications of the product. These documented specs are open for the distributors and customers, to avoid any fault or mis-ordering process.
3.21. Sweat Effect: During measurement and packing processes that require continuous measurement, handling, and packing. The use of light-cotton gloves, depending on the structure of the product, will prevent the effect of sweat that may occur.
3.22. Sensitive Coated Products: These are products coated with a special process to increase their resistance to external factors such as heat and oil.
4. SUPPLIER TYPES
In the scope of LORAN's business capabilities, the Suppliers are classified into 4 Groups:
4.1. Manufacturer or Distributor,
4.2. Raw Material Supplier,
4.3. External Laboratory,
4.4. State Bodies,
5. NORMATIVE DOCUMENTS
LORAN uses the following documents to prepare this manual.
5.1. AS9100 Rev.D: Quality Management Systems - Requirements for Aviation, Space, and Defense Organizations
5.2. AS9120 Rev.B: Quality Management Systems – Requirements for Aviation, Space, and Defense Distributors
5.3. AS13000 2014: Problem Solving Requirements for Suppliers
5.4. AS9131 Rev.D: Aerospace Series - Quality Management Systems - Nonconformity Data Definition and Documentation
5.5. AS6174 Rev.A: Counterfeit Materiel; Assuring Acquisition of Authentic and Conforming Materiel
5.6. AS6832-2020: Counterfeit Materiel, Assuring Acquisition of Authentic and Conforming Fasteners
5.7. AS9138-2018: Aerospace Series - Quality Management Systems Statistical Product Acceptance Requirements
5.8. AS9146-2017: Foreign Object Damage (FOD) Prevention Program - Requirements for Aviation, Space, and Defense Organizations
5.9. AS6174 Rev.A: Counterfeit Material, Assuring Acquisition of Authentic and Conforming Material
5.10. AS9163-2022: Aerospace Series - Certification of Conformity Requirements
5.11. AS6416-2022: Bolts, Screws, Studs, and Nuts, Definitions for Design, Testing and Procurement
5.12. ARP9134 Rev.A: Supply Chain Risk Management Guideline
5.13. ISO17025-2017: General requirements for the competence of testing and calibration laboratories
5.14. ISO10002-2018: Quality management — Customer satisfaction — Guidelines for complaints handling in organizations
5.15. ISO31000-2018: Risk management — Guidelines
5.16. ISO 10007-2017: Quality Management - Guidelines for Configuration Management
5.17. ASTM D3951-18R23: Standard Practice for Commercial Packaging
5.18. MIL-STD-129-R 2023: Military Marking for Shipments and Storage
5.19. MIL-STD-2073-1: Standard Practice for Military Packaging
5.20. TB-003 Rev.A: Counterfeit Parts and Materials Risk Mitigation
5.21. CMB5A Rev.A: Configuration Management Requirements for Subcontractors/Vendors
6. GENERAL QUALITY REQUIREMENTS
6.1. Quality Management System Requirements
|
AS9100 REV.D |
AS9120 REV.B |
ISO9001 – 2015 |
ISO17025 – 2017 and/or NIST |
NADCAP |
APPLICABLE TESTS |
MANUFACTURER |
Mandatory |
|
|
|
Primary Preference |
NDT – DT Mandatory |
SUPPLIER – Distributor |
|
Mandatory |
|
|
|
NDT Mandatory |
SUPPLIER – Raw Material |
|
Mandatory |
|
|
|
NDT Mandatory |
SUPPLIER – Heat Treatment |
Primary Preference |
|
Mandatory |
|
Primary Preference |
NDT – DT Mandatory |
SUPPLIER – Coating / Plating |
Primary Preference |
|
Mandatory |
|
|
NDT – DT Mandatory |
SUPPLIER – Blasting |
Primary Preference |
|
Mandatory |
|
|
NDT – DT Mandatory |
SUPPLIER – Welding |
Primary Preference |
|
Mandatory |
|
Primary Preference |
NDT – DT Mandatory |
EXTERNAL LABORATORY |
|
|
Primary Preference |
Mandatory |
Primary Preference |
NDT – DT – CALIBRATION Mandatory |
6.2. Control of Documents
6.2.1. The supplier is responsible for checking the documents in their possession regarding those flowing down on purchase orders and obtaining the necessary standards.
6.2.2. The supplier must establish an active document control mechanism in their quality management system to confirm the document's validity and traceability.
6.2.3. The supplier should ensure control of documents and data to their suppliers in controlled distribution. Data security is a mandatory obligation for the supplier.
6.2.4. The supplier must maintain their project management possession documents and data for a minimum of 10 years period from their product delivery date.
6.2.5. On-Site Acceptance: Before dispatching the product from the supplier's warehouse, sometimes LORAN may need to approve the products and documents at the supplier's place. LORAN must indicate the on-site acceptance condition on the purchase order document.
6.3. Traceability Documents and Flow Down Chart
6.3.1. Traceability is documentation and flown-down tracking process, and all companies need to supply exact traceability documents with true tracking references.
6.3.2. Traceability is documentation and flown-down tracking process, and all companies need to supply exact traceability documents with true tracking references.
6.3.3. Traceability documents must be printed on the company's letterhead paper and must include a minimum of the following information:
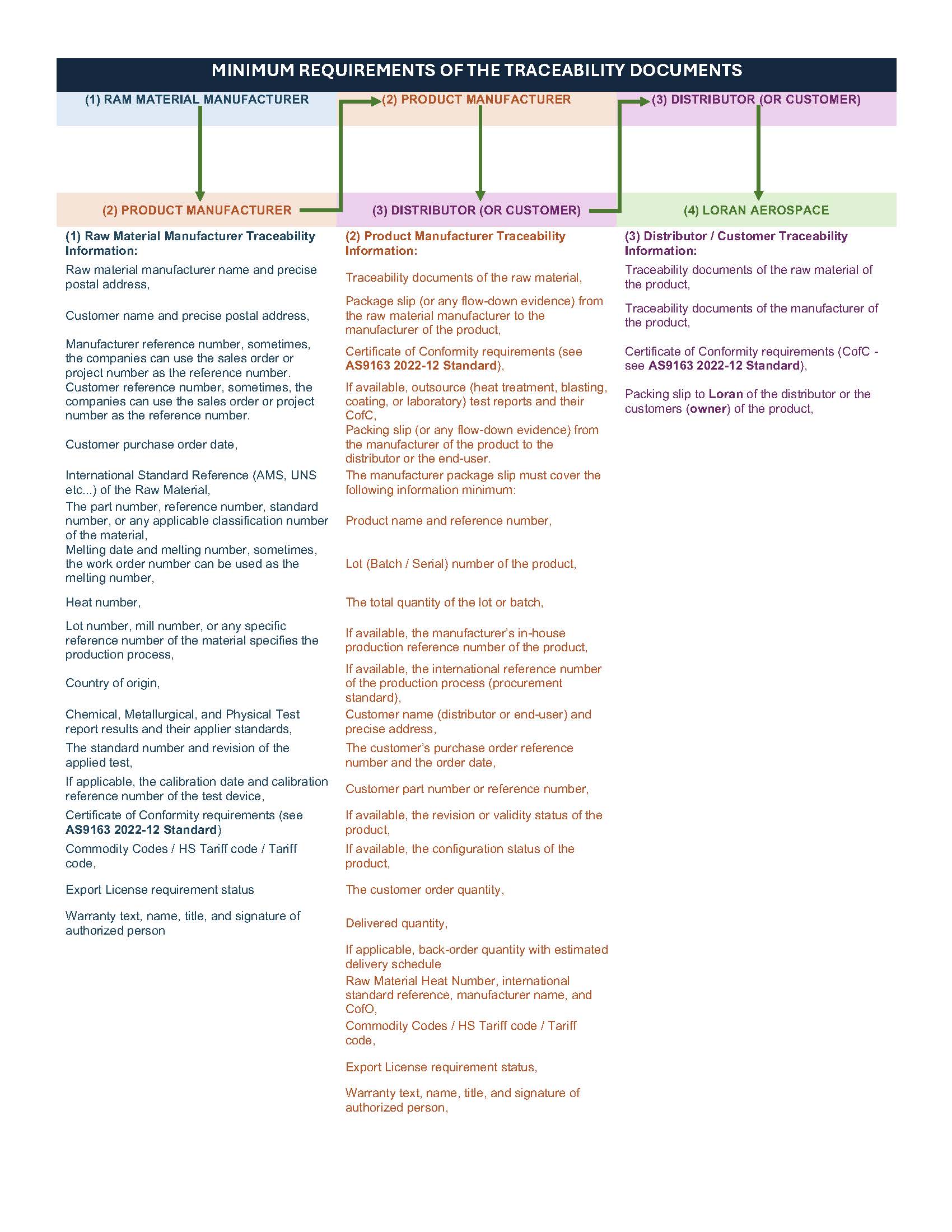
6.4. Product Conditions and Traceability
6.4.1. FACTORY NEW (FN): The product received from Original Equipment Manufacturers (OEM) or Main Manufacturer or Authorized Distributor in original package with CofC and FAA/EASA (if applicable).
6.4.2. NEW / UNUSED (New): For products that do not have shelf-life restrictions, the product must be in its original package and unused condition, even if the production date is old. The supplier can be OEM, authorized distributor or any supplier, and the supplier CofC must be received with the package.
6.4.3. NEW SURPLUS (NS): The product received from other than OEM or authorized distributor, the product should be in the original package, and the vendor CofC must be received with the package.
6.4.4. OVERHAULED (OH): The product has been overhauled by an authorized repair shop; the repair shop must supply a Tear-Down Report, Accident Commitment, and Overhaul Reports with its CofC and FAA/EASA certificate.
6.4.5. OBSOLETED PART, SERVICEABLE (SV) and AS-IS (AR): Loran does not supply products with SV or AR conditions.
6.5. Nonconformity Claims
6.5.1. With regards to the nonconformity claims, Loran accepts the requirements texted in the "AS9131 Rev.D" Standard.
6.5.2. Any nonconforming materials, parts, assemblies, subassemblies, systems, subsystems or services shall be documented and reported to Loran within 24 hours.
6.5.3. No deviation will be considered approved or be allowed to ship to Loran without written confirmation from Loran.
6.5.4. All nonconforming materials, parts, assemblies, systems, subsystems, or services shipped to Loran shall be clearly identified as such.
6.5.5. Unless otherwise specified in the contract with the manufacturer, the below-specified nonconformity procedure may be applied before the product dispatch approval step.
6.5.6. The manufacturer must fix the non-conformance issue in a maximum of 2 weeks, if the manufacturer can not provide enough corrections on the products in this period, Loran will keep the order cancellation right. If the manufacturer needs more than 2 weeks to provide enough corrections, the manufacturer must need Loran's approval on this correction.
6.6. Chemical Products:
The supplier must ensure that it provides at least the following:
6.6.1. FOR SHELF-LIFE AND AGE-CONTROLLED MATERIALS, THE SUPPLIER SHALL ENSURE THAT AT LEAST 75% OF THE MATERIAL LIFE IS REMAINING AT THE TIME OF DELIVERY, THIS REQUIREMENT MAY BE WAIVED BY LORAN MANAGEMENT.
6.6.2. Unless otherwise specified, LORAN accepts IATA regulations for the products that are classified as Dangerous Goods. All of LORAN's supplier companies must implement the IATA regulations for all types of HAZ-MAT classified products. Codification of the product and package is under the supplier’s responsibility. (for more details about the codification, please visit the IATA website - https://www.iata.org/en/publications/directories/code-search/)
6.6.3. The packaging must be of good quality, strong enough to withstand the shocks and loadings normally encountered during transport, including trans-shipment between transport units and between transport units and warehouses, as well as any removal from a pallet or overpack for subsequent manual or mechanical handling.
6.6.4. Packaging must be constructed and closed so as to prevent any loss of contents that might be caused under normal conditions of transport, by vibration, or by changes in temperature, humidity or pressure.
6.6.5. The packaging must consist of three components:
6.6.5.1. Primary Receptacle(s): Primary receptacles must be packed in secondary packaging in such a way that, under normal conditions of transport, they cannot break, be punctured, or leak their contents into the secondary packaging.
6.6.5.2. Secondary Packaging: Secondary packaging must be secured in outer packaging with suitable cushioning material. Any leakage of the contents must not compromise the integrity of the cushioning material or of the outer packaging.
6.6.5.3. Rigid outer packaging
6.6.6.The packing types of the liquid and solid products are to be similar to the regulations published by IATA. (please visit IATA website - https://www.iata.org/contentassets/b08040a138dc4442a4f066e6fb99fe2a/dgr-64-en-pi650.pdf)
6.6.7. The item list of the shipment includes An Itemized List of contents must be enclosed between the secondary packaging and the outer packaging.
6.6.8. At least one surface of the outer packaging must have a minimum dimension of 100mm x 100mm (3.93701” x 3.93701”).
6.6.9. The completed package must be capable of successfully passing the drop test described in 6.5.4.4 as specified in 6.5.4.2 except that the height of the drop must not be less than 1.2 m. Following the appropriate drop sequence, there must be no leakage from the primary receptacle(s) which must remain protected by absorbent material, when required, in the secondary packaging.
6.6.10. Package labeling and marking must be suitable with IATA regulations. For transport, the mark must be displayed on the external surface of the outer packaging on a background of a contrasting colour and must be clearly visible and legible.
6.7. Configuration Management
6.7.1. Loran carries out configuration management according to the ISO 10007:2017 At the same time, Loran also implements the following technical guidelines when determining its configuration policy:
6.7.1.1. "Piece Parts" Requirements are clarified in the SAE technical report of the "CMB5 Configuration Management Requirements for Subcontractors/Vendors Rev.A 2014" of when determining its configuration policy.
6.7.1.2. SCMH 7.5.3 Configuration Management Guidelines (Rev. B 2021)
6.7.2. The supplier is required to have a configuration management system that provides the internal and external documents and revision levels applicable to a particular purchase order. The configuration management applied by the supplier must be suitable to at least ISO 10007-2017 standard.
6.7.3. Unless specified in the manufacturer's technical documentation or unless specifically stated in the LORAN 'purchase order, the supplier's responsibility is to supply the latest version of the product manufactured by the manufacturer, depending on the product’s descriptive reference information.
6.8. Foreign Object Damage (FOD)
6.8.1. Another important point for Loran while managing the product acceptance process is the nonconformities arising from "Foreign Object Damage (FOD)." Loran bases the FOD Requirements on the criteria described in AS9146 2017-04.
6.8.2. The primary preference for LORAN is that the supplier has active and applicable FOD management.
6.8.3. Loran considers the following situations as non-conformance caused by FOD:
ü package not fully closed,
ü the presence of any foreign object other than the product in the packaging,
ü the packaged product is moist,
ü the packaged product is rusty,
ü the packaged product is broken or deformed,
ü unlabeled packaged products,
ü products with illegible or torn labels,
6.8.4. Dust, sweat, and handprint preventing equipment must be used in the packaging of the products, and the supplier's packaging area must be structured accordingly.
6.8.5. For handling, personnel shall wear gloves, such as cotton gloves, fine-grained leather gloves, or gloves made of any other soft and light material, to prevent scratches, oxidation (tarnishing), and color tone change.
6.9. Prohibited Practices
6.9.1. Material substitution by Supplier is forbidden for all materials, parts, assemblies, subassemblies, systems, subsystems, or services supplied to Loran.
6.9.2. Scrap: The Supplier shall return any furnished materials, parts, assemblies, subassemblies, systems, subsystems or services that the supplier has dispositioned as scrap to Loran. Loran shall determine whether the proper disposition will be scrapped.
6.9.3. Repair: The supplier shall not repair a product without Loran's prior written approval.
6.9.4. Rework: The supplier shall not perform work outside the specific specification limits.
6.9.5. Re-Sell of Rejected Items: The supplier shall clearly identify the products rejected by LORAN or any customer, and the rejected products are strongly prohibited from reselling in the market.
6.9.6. Conflict Minerals: The supplier must comply with the requirements of the Dodd-Frank Act on Conflict Minerals (for more details, please visit: https://www.sec.gov/newsroom/press-releases/2012-2012-163-related-materials or https://ec.europa.eu/commission/presscorner/detail/fr/memo_14_157). If a conflict mineral is used in the product, and if the supplier detects this situation before or after product delivery, Loran must be notified within a maximum of 60 days after this determination.
6.9.7.&